Frequently Asked Questions
What do we buy?
We purchase ceramic and metal foil catalytic converters, as well as oxygen sensors.
What is recycled from catalytic converters and why is it worthwhile?
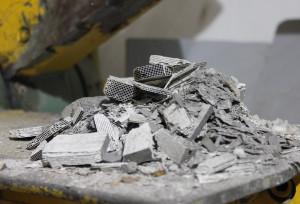
“Pieces of a ceramic monolith. The most valuable part of a catalytic converter, which contains the precious metals.”
The most valuable part of the whole converter is the catalyst, which is composed of precious metals – platinum, palladium and rhodium. Although these metals have similarities, some of their qualities differ – for example, rhodium is the best metal for removing nitrogen oxides while platinum is the best catalyst for completing the burning of fuel in the exhaust. Because of varying requirements for the converter, there are numerous combinations of platinum, palladium and rhodium in use.
Recycling these metals from converters takes a lot of effort but their rarity in nature and their high value makes it economically feasible.
What is a ceramic catalytic converter and how is its value determined?
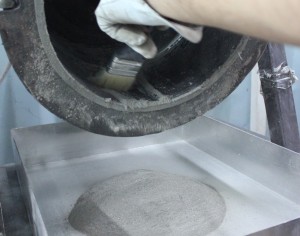
“In order to analyze the content of precious metals, ceramics must be ground and mixed meticulously.”
It is a converter with ceramic-based monolith – most often made of a mineral called cordierite. Over 90 percent of automotive catalytic converters worldwide are ceramic, thus making it our most common purchase material.
A ceramic catalytic converter is made by covering the honeycomb-like, porous ceramic monolith with oxide washcoat, which acts as support for the precious metal particles. These particles act as the active catalyst, yet typically only constitute about 1% – 2% by mass in the washcoat (not the whole converter!). The monolith is then installed into a steel case and becomes a part of the exhaust system. As for all catalytic converters, the large active surface area ensures efficiency, which is vital when high amounts of pollutants are to be converted in a fraction of a second.
When a ceramic converter is due to be recycled, it is firstly cut open and the ceramic monolith is removed and ground to fine powder. Then its elemental composition can be estimated using different methods of X-ray spectrometry before starting the actual recovery of the metals. While it is not compulsory to start the process of recycling by grinding, it is the best method for determining the value of the converter in advance of chemical recovery and allows converters to be bought without long delays.
What is a metal foil catalytic converter and how is it recycled?
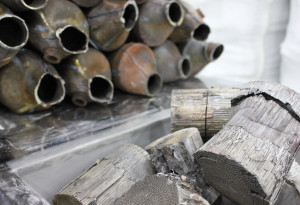
“Whereas the function of metal foil converters is the same as of the ceramic ones, the treatment needed for analysis and recycling is largely different.”
Metal foil catalytic converters serve the same function as their ceramic counterparts – the main difference being the monolith on which the catalyst is deposited. Instead of a porous ceramic monolith, a honeycomb made of metal foil is used. A specific alloy, Kanthal, which consists of iron, chromium and aluminum, is often used due to its high resistance to heat.
The recycling process of metallic catalytic converters is more difficult than that of ceramic ones because the metal foil cannot be ground into powder in such a manner as is done with ceramics. Instead, by extensive grounding and milling the washcoat is removed from the metal foil support and then recycled.
What are oxygen sensors?
For a catalytic converter to work properly the ratio of fuel to air must be strictly controlled in the burning chambers. Therefore, an oxygen sensor is used to measure the quantity of oxygen entering the catalyst. It provides feedback to the control systems, telling them to increase or decrease the aforementioned ratio. Sometimes a second sensor is used to check the state of the catalytic converter by measuring the oxygen content in the exhaust leaving the converter.
Oxygen sensors also contain platinum, which is worth recycling.
What determines the price of a converter?
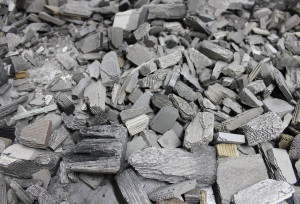
“Precious metal content can sometimes vary even between very similar converters, therefore, when we know that there is some uncertainty in the price of goods being purchased, we suggest our clients use the “Direct Processing” method.”
Two factors – the precious metal content and its weight – depend only on the converter itself. Furthermore, even converters of the same model can have slight differences owing to subtleties of production, exploitation and the composition of the fuel used.
The third factor in calculating the price are the market prices of platinum, palladium, and rhodium. As the prices of the metals themselves change, so do the prices of catalytic converters.